I'm writing in hopes one or more of you will jump in here and lend some of your expertise to the business of making aileron, rudder and elevator control horns.
Now, I'm as much a romantic as the next guy and if making the horns according to the plans is a nod to Bernie's way of doing it back in 1929....that's fine with me. But please tell me this: Why in the heck (especially with the aileron horns) are they made out of TWO thicknesses of steel...mirrored next to each other, then sort of "puffed out in the middle", hollow like, until they look like a croissant, then their edges welded all around?
When I built the Corben Jr. Ace (another open cockpit parasol) those control horns were simply ONE thickness of metal, bent where they needed to attach to the wood, with a thickness about what TWO pieces of Piet metal wind up equaling.
What am I missing here?
Are/have all you guys done them just like the plans show or have you done them in some other way? Who can explain WHY Bernie did them this way?
Will the Piet Gods strike me out of the sky if I deviate from the original look or......what?
Thanks in advance.
About those control horns...
Re: About those control horns...
While they do take a bit more effort and time to make than just one flat piece of metal, they are not hard to make and they do actually wind up being lighter and stronger.
There are a couple of good examples of how to make them on the West Coast Piet site.
There are a couple of good examples of how to make them on the West Coast Piet site.
-
- Posts: 112
- Joined: Fri Aug 31, 2018 9:23 am
Re: About those control horns...
Thanks for the reply. I'll try to find the West Coast Piet site now.
Brian
Brian
Re: About those control horns...
Looking at the way the control cables are routed, there is a sideways component to the force on the horn. A solid flat plate will either warp slightly or be thick enough that there is a bit of a weight penalty. Extra weight out on the tail where three of the horns are is definitely undesirable for the CG. I don't know how much warping is tolerable but I suspect it doesn't take much to affect the tension of the cables. The plans call for 2 22 gauge plates for the sides of the horn and a 16 gauge plate for the brace. So the sides are the same thickness and there combined thickness is equal to the 16 gauge plate. Forming the leading edge of the horns is really not difficult, I took an 1/8" diameter rod and welded it to the edge of a 1/4" plate so that it was flush with face of the plate. I sandwiched the horn in a vice with the plate and hammered the edge of the horn half way around the rod. You can hammer on it and then shift the horn template around and hammer on it again to get everything just right. 1/8" doesn't sound like much but it adds a lot to the rigidity of the horn.
-
- Posts: 112
- Joined: Fri Aug 31, 2018 9:23 am
Re: About those control horns...
ArthurD: Now THAT makes a whole lot more sense then just making a hollow control horn for no apparent reason other than "they look really neat".
And I like the idea of forming them around that rod.
One other thing? One of our members welded his edges together withOUT welding rod....just "fusion welding" by melting the two pieces with heat only. His beads looked great.
Any thoughts anyone?
Thanks for all that.
And I like the idea of forming them around that rod.
One other thing? One of our members welded his edges together withOUT welding rod....just "fusion welding" by melting the two pieces with heat only. His beads looked great.
Any thoughts anyone?
Thanks for all that.
Re: About those control horns...
On the horns the trailing edge is an edge joint and as you move around toward the center of the leading edge it becomes more of a butt joint.
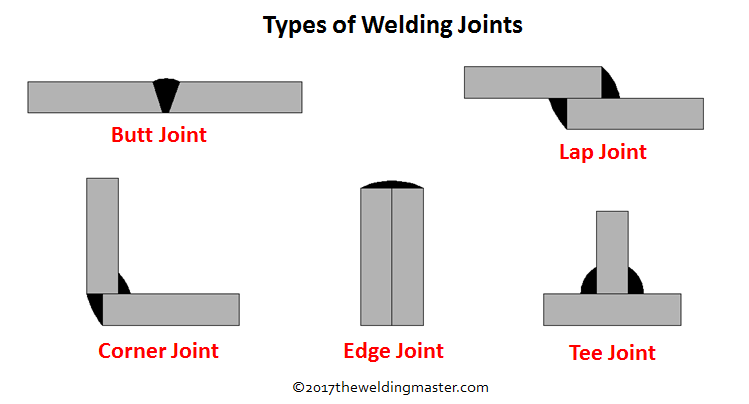
You can get away with not using filler on edge joints in material this thin. It's actually pretty easy to do because there's nowhere for the puddle to go other than staying right on the edge. On the butt joint it requires perfect fit up and perfect technique to get away with an autogenous weld. If you're not careful, and by careful I mean perfect, you will melt away the edges of one or both plates before they merge and you end up with a hole. Filler rod will make it much easier to get good fusion without risking burning through.
Source: I'm a welding engineer.
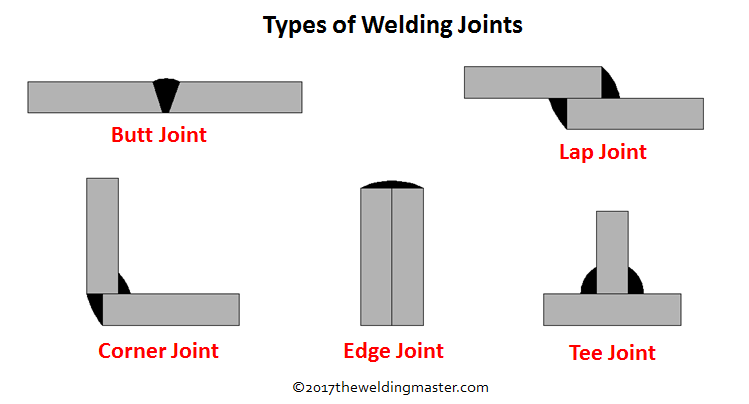
You can get away with not using filler on edge joints in material this thin. It's actually pretty easy to do because there's nowhere for the puddle to go other than staying right on the edge. On the butt joint it requires perfect fit up and perfect technique to get away with an autogenous weld. If you're not careful, and by careful I mean perfect, you will melt away the edges of one or both plates before they merge and you end up with a hole. Filler rod will make it much easier to get good fusion without risking burning through.
Source: I'm a welding engineer.
Re: About those control horns...
Just do it, you will feel so good when finished and showing them off (like now).
RH
RH
Re: About those control horns...
Those are some mighty purty models of stealth bombers ;o)